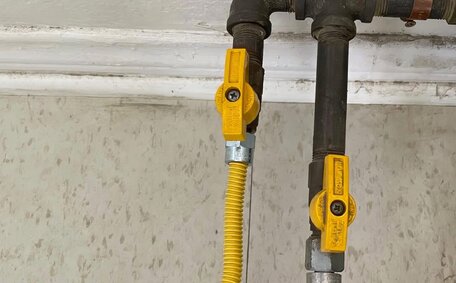
Natural Gas vs. Propane: What’s the Difference?
Propane and natural gas are popular fuel sources, but have different origins and properties. Propane delivers more BTUs per cubic foot. Natural gas is piped underground to homes.
Read MoreGas pipelines are typically designed to have a functional lifespan of around 50 years. However, the actual longevity can vary quite significantly depending on several key factors. Well-maintained pipelines in low-risk areas may continue operating safely for 60 years or longer before needing replacement.
Conversely, pipelines in regions prone to ground shifts or corrosion may require earlier retirement or renewal, sometimes in as little as 30-40 years. Pipelines constructed years ago, predating modern construction standards and safety regulations, often exhibit shorter usable lifespans.
The natural gas industry uses 50 years as a general benchmark for pipeline lifespan planning. But regular maintenance and inspection programmes are crucial to achieve this. Necessary upgrades and repairs throughout decades of use enable pipelines to keep performing safely and efficiently.
There are several key factors that can impact the lifespan and longevity of gas pipelines:
Considering these key factors right from the design and construction phase and maintaining vigilance through a pipeline’s operating life are vital to maximise longevity.
The most common materials used for gas pipelines in Australia are steel and polyethylene plastic. Steelpipelines tend to have longer design lifespans, while plastic mayneed replacing sooner.
High pressure gas transmission pipelines transporting natural gasover long distances are typically constructed from carbon steel orstainless steel. These steel pipelines have an expected lifespanof 50-80 years if properly maintained.
Local gas distribution networks use a mix of steel and plasticpipes to supply homes and businesses. polyethylene pipeshave an anticipated lifespan around 50 years. Olderunjoined steelmains may last 60+ years barring corrosion.
The longevity of any pipeline relies heavily on material durabilityas well as operating conditions. External environmental factorssuch as soil acidity and internal abrasionfrom gas flow cumulativelyreduce integrity over time. Proactive maintenance and replacements ofolder sections enables gas networks to safely meet demand beyondtheir initial design life.
The high-pressure operation of gas pipelines contributes to their functional lifespan limitations over decades of use. As natural gas flows through the enclosed pipeline system at up to 2,000 pounds per square inch (psi), intricate stress forces act on the steel or polyethylene pipe walls.
Over time, these stresses cause material fatigue and microscopic cracks which may worsen despite corrosion protection measures. Areas where pipelines bend or join are especially vulnerable to concentrated wear from persistent high-pressure loads.
Pipeline operators aim to keep gas flow pressures lower than the maximum design threshold to minimise pipe wall stress. However, varying demand cycles, irregular gas supplies, and network balancing needs make some pressure fluctuations inevitable.
While steels used in modern gas pipelines are durable, decades of cumulative stress coupled with corrosion will necessitate inspections and component replacements to sustain safe operations. New technologies that enable strength tests and pressure modifications based on real-time pipeline wall monitoring can optimise longevity.
Corrosion poses one of the biggest threats to the longevity of metal gas pipelines. Over decades, chemical reactions slowly degrade the pipe’s steel walls from both the interior and exterior surfaces.
On the outside, soil characteristics including acidity, moisture, and conductivity contribute to corrosion. Pipelines installed in highly corrosion risk areas tend to have shorter lifespans of 35-45 years unless the material quality is bolstered.
Internally, chemical compounds present in natural gas can accelerate corrosion rates especially at high temperatures and pressures. Areas with irregular gas flow or lengthy stagnant periods also see elevated corrosion risks.
Pipe joints and seams are particularly vulnerable to corrosion issues which weakens these high-stress domains. Maintaining tightly sealed Lot records and component traceability enables proactive joint repairs.
Modern pipeline corrosion protection methods include durable epoxy coatings and impressed their sacrificial anodes. Regular inspections also facilitate early maintenance interventions. As pipelines age however, full sections may need replacing to prevent perforations.
Several key maintenance practises can help extend the functional lifespan of gas pipelines by decades:
While individual pipe sections may be replaced, sustained maintenance and safety upgrades ensure gas pipelines can safely supply households and businesses even when they are no longer in their prime, extending well beyond 50 years.
Regular inspection and monitoring is crucial to assess pipeline integrity as networks age. Australian standards such as AS 2885 mandate operators perform safety checks to enable proactive repairs.
Techniques like inline inspection ‘pigs’, hydrostatic testing, direct assessment and patrols identify issues before they endanger nearby communities. Smart sensor networks also facilitate real-time monitoring.
Inline inspection gauges or ‘pigs’ travel inside pipelines to precisely locate corrosion, cracks and wall damage using ultrasound, magnetic flux or other methods. Periodic pigging runs chart pipe wall thinning trends.
Hydrotesting involves pressurising isolated pipe sections with water to stress walls to their limit without gas, checking for leakage. New technologies enable targeted in-service hydrotesting too.
Close-interval potential surveys assess external corrosion by detecting charge leakage through pipeline coatings. Direct current voltage gradient tests check cathodic protection efficacy.
Regular foot, vehicle or aerial patrols also check surface conditions near pipelines. Thermal scanning detects subtle underground leakage. All inspection data informs risk-based maintenance needs before major failures.
Pipeline operators take both reactive and proactive approaches to repairs and replacements to sustain integrity. While new pipelines are designed for 50+ year lifespans, extensive repairs or section replacements may be needed well before decommissioning.
Significant defects like deep corrosion pits or cracking identified during inspections may require immediate repairs based on risk. However minor issues may be monitored and bundled for later maintenance. Components like valves, anodes and seals also undergo selective replacement.
Proactive small repairs reduce expansion rate of defects. But if over 60% of a pipeline’s surface area needs repairs, full section replacement is often preferable. Pipes under high stress near facilities also warrant proactive replacement.
When pipeline damage assessment deems conditions unsafe per standards or further repairs are uneconomical, replacement is commissioned even if the asset hasn’t reached its intended lifespan. With new materials that meet modern specifications, it’s expected that a pipeline would support continued operations well beyond another 50 years.
Several national and state regulations dictate the safe operation, maintenance, and longevity of gas pipelines across Australia. Adhering to these stringent safety standards enables the extended lifespan of assets while protecting nearby communities.
Key regulations include AS 2885 - Pipelines - Gas and Liquid Petroleum covering materials, design, construction, operations, maintenance and decommissioning. Jurisdictional codes like the NSW Gas Supply (Safety and Network Management) Regulation 2013 also apply in alignment.
These codes mandate rigorous corrosion and leakage monitoring, hazard identification, emergency response protocols, plus validation of technical competencies. Standards get updated periodically, compelling upgrades.
Breach penalties compel compliance.
However, progressive operators aim beyond mere rule compliance, implementing safety management systems spanning pipeline lifecycles. They undertake risk assessments considering pipeline environments and interactions with the public or workers. Higher safety targets drive lifecycle extension investments like corrosion-resistant coatings.
Ultimately, meeting evolving safety regulations over time enables the safe and optimal utilisation of pipeline assets over their lifespan of 50 years or longer through appropriate maintenance protocols.
When gas pipelines near the end of their functional lifespan after 50+ years, decommissioning processes are initiated to retire them safely. As no definitive federal or state laws define decommissioning procedures, pipeline owners develop custom plans in consultation with authorities.
Key steps involve permanently isolating the pipeline from active networks and rendering it inert. Any residual gas or liquids are flushed out using air, water or chemical pigging. The line pressure is then reduced to zero.
Another method is in-place abandonment, which fills the pipeline with concrete or an inert solid. This prevents future use or accidental damage. The pipeline owner continues monitoring for safety per asset retirement obligations.
Visible above-ground fixtures and pipe sections get dismantled and removed first. Buried lines are left underground unless posing an environmental issue. Easement agreements may however compel owners to dig up and extract retired pipe sections.
With specialised processes tailored to each situation, ageing gas pipelines ultimately undergo safe retirement from infrastructure delivering household energy needs. Decommissioning enables their replacement with modern, efficient assets.
When gas pipelines near the end of life after 50+ years of service, abandonment requires careful planning to minimise safety risks. Pipeline owners must decide between removal or decommissioning in place based on pipe location, condition and community impacts.
Removing the buried pipeline avoids potential land erosion or third-party construction damage issues in the future. However, this disruptive process risks pipe damage during extraction, and disturbance of surrounding infrastructure. Residual gas pockets also pose risks for workers and the public.
Conversely, abandoning pipes underground with concrete plugs seems convenient but has long-term community safety implications. Over decades, records fade and pipes left in place may get accidentally struck during unrelated excavations or utility works. Pipeline markers and locator wires help, but aren’t failsafe.
Thorough planning, risk-impact analysis and community consultations enable customised abandonment strategies per situation. GPS mapping and sensor technologies allow remote monitoring of decommissioned lines. Ultimately though, safely retiring unstable pipelines to avoid future public hazards remains the priority, by removal if necessary.
Propane and natural gas are popular fuel sources, but have different origins and properties. Propane delivers more BTUs per cubic foot. Natural gas is piped underground to homes.
Read MoreUpgrading a gas meter improves safety and may be necessary over time. Our experienced team can guide you through the process, costs and timeframes involved to upgrade your gas meter.
Read MoreIf pipe relining fails due to severe damage, replacement may be required. We provide affordable pipe repairs in Sydney without excavation. Call today for pipe assessments. Our expert team will determine if pipe relining or full replacement is needed.
Read MoreWoollahra, 2025 NSW
We will call back as soon as possible.